The die casting machine is one of the most efficient casting machines. Depending on the type of die casting, a cold chamber die casting machine or a hot chamber die casting machine is required. How does the die casting machine operate? When the machine is running, a safety door should be used to prevent the molten metal from the parting surface of the mold from splashing out and hurting the operator. It is strictly forbidden to short-circuit the safety door limit sensing device. Before injection, the model must be heated to the specified temperature, and then the metal solution can be pressed... Let's learn about the safety operation rules of the die casting machine.
Safety operation rules of die casting machine
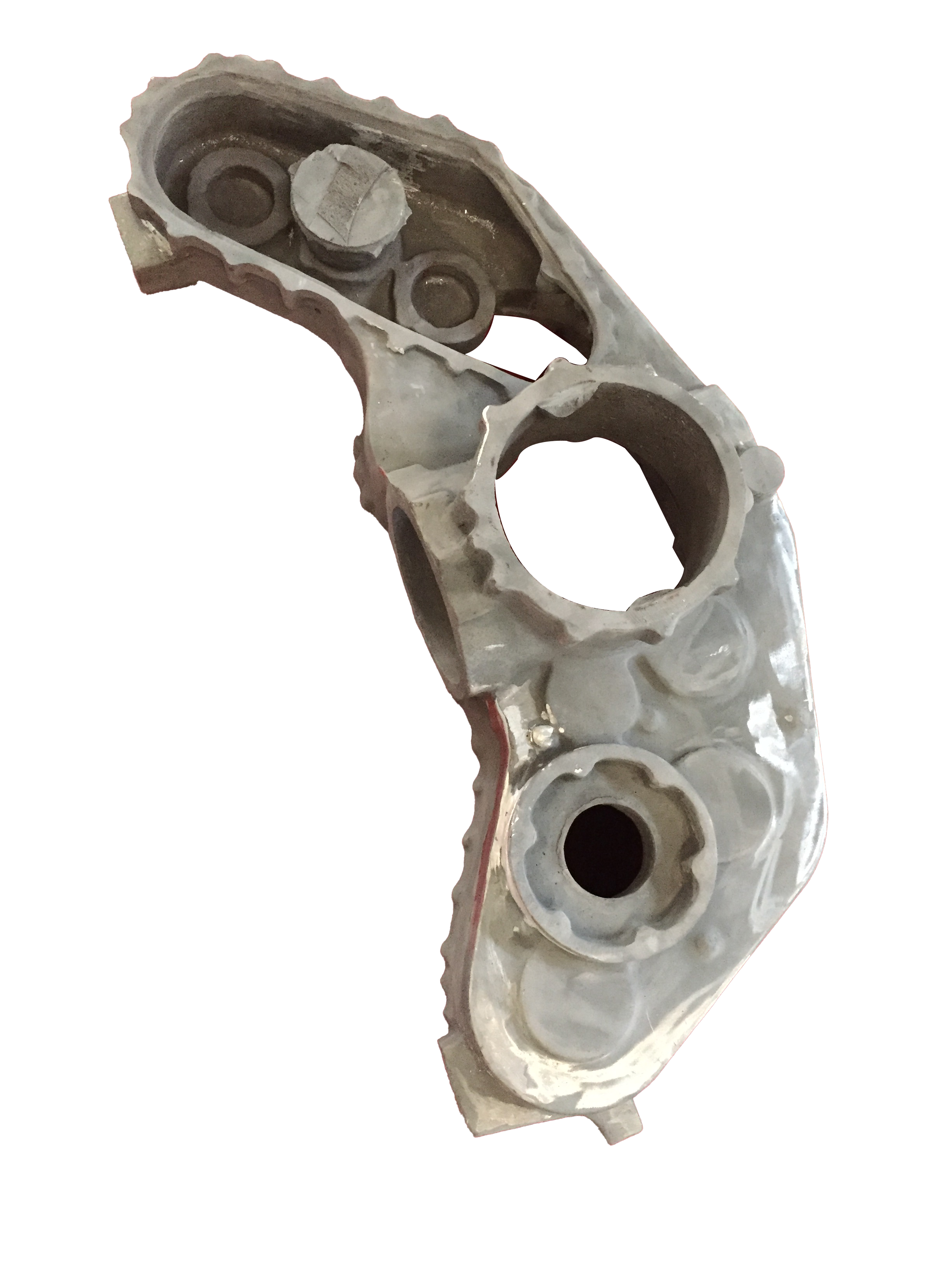
- A safety door should be used when the machine is running to prevent the molten metal from the parting surface of the mold from splashing out and hurting the operator. It is strictly forbidden to short-circuit the safety door limit sensing device.
- When the machine is turned on every day, the appearance of each part of the machine should be checked for cleanliness before turning on the machine.
- According to the requirements of the lubrication diagram, lubricate each lubrication point regularly, especially the lubrication of the clamping mechanism and the guide rail. Lubricate several times before going to work every day, and check whether the lubricating oil is in place, and then start the machine.
- After the machine is started, it should be cooled with water to prevent the oil temperature of the hydraulic oil in the fuel tank from rising. The water source should be turned off after getting off work, especially in winter. The cooler of the machine needs to be cooled with water. When necessary, the die also needs to be cooled by water.
- The power supply of the machine must be turned off when cleaning the machine or repairing the mold. Also turn off the power after getting off work.
- When the machine fails or the alarm signal sounds, the pump should be turned off, the power supply should be cut off, and the machine should be overhauled.
- When installing the die-casting mold, the machine should use the "manual" working system to adjust.
- Under the premise of the permissible range of die-casting process and ensuring that the material does not run out during production, the clamping force should be appropriately reduced to prolong the life of the clamping toggle structure.
- When dismantling any high-pressure components (such as hydraulic valves, pipes, etc.), there may be residual pressure inside, so it is not advisable to over-speed when loosening the screws, and the screws should be loosened only after the residual pressure is discharged. For the relevant hydraulic parts, the unloading valve should be opened first, and the high-pressure liquid in the accumulator should be completely discharged before disassembly, otherwise it will cause danger.
- If the machine needs to stop for a long time, the pump should be turned off.
- If any problem is found during the operation, the protective door should be opened to stop the working cycle immediately, and then check the cause and repair the fault.
- The electric box should always be protected from moisture and heat to ensure the normal operation of electrical components.
- The oil pump suction port filter should be cleaned frequently to ensure that the filter element is clean.
- The lubricating surfaces on the moving parts of the machine should be dusted frequently to prevent unnecessary wear.
- The non-parallelism between the head plate and the middle plate of the machine has been adjusted before leaving the factory. If it has been used for a period of time or after major repairs, it must be re-measured. When adjusting, first loosen the Colin column nut pressure plate, and turn the nut slightly for re-adjustment.
- Every time the pressure oil is replaced, the filter in the fuel tank should be carefully cleaned.
- When adjusting the thickness of the die, do not start the die-adjusting motor when the die is in a closed state, otherwise the die-adjusting mechanism will be damaged.
- This machine adopts a piston accumulator. The accumulator is equipped with a charging gas valve. When charging, connect the charging connecting pipe. The other end is connected to the nitrogen cylinder. The accumulator can be charged with nitrogen, the charging pressure can be observed with a pressure gauge, when the required pressure is reached, close the charging valve, turn off the nitrogen bottle switch, and then loosen the charging connecting pipe.
- You can press the button of the lubricating pump by hand to let the oil pump fill the lubricating points with oil. When fully automatic, the oil pump will supply oil according to a certain number of mold clamping times or a certain period. (selected by the operator)
Conclusion
For more information about cost of die casting machine,material used in preparation of die casting mould,die casting components manufacturers, we are glad to answer for you.