When we manufacture an item, everyone will have many problems. Among them, the problem of temperature is inevitable. If the temperature is insufficient, the quality will not be good. If the temperature is too high, it will be very easy to break. The problem, today's net editor will share with you how to control the temperature in the case of injection mold manufacturing.
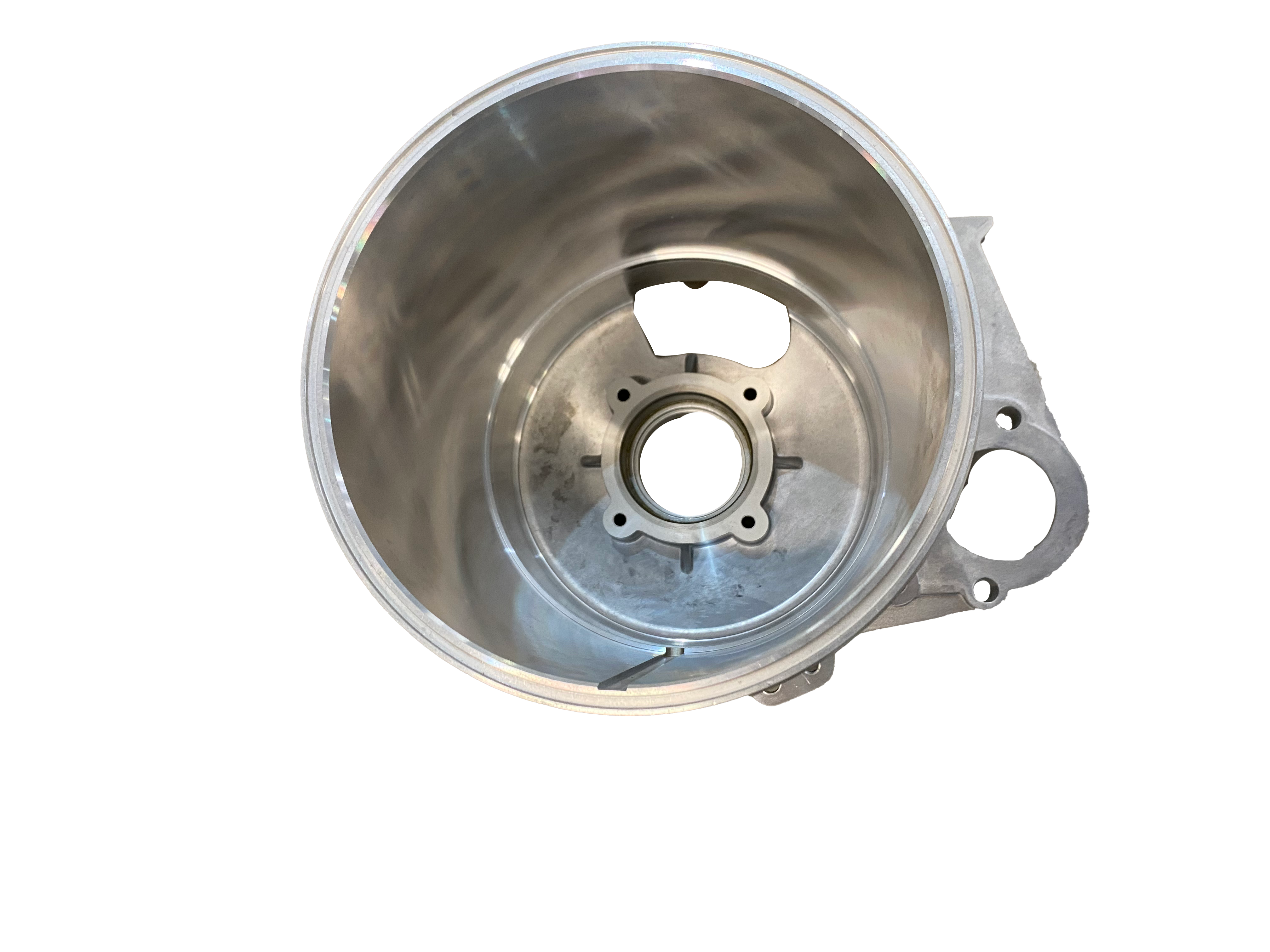
How to control the temperature in the production of die casting molds
Manipulating the ambient temperature of zinc alloy die castings are particularly important for producing high quality castings. Unbalanced or inappropriate temperature of zinc die-casting molds can also cause unstable casting specifications. During the processing, the castings are deformed, resulting in defects such as pressing, sticking, surface dents, shrinkage porosity, and hot bubbles.
When the temperature difference of the zinc injection mold is large, it will jeopardize the independent variables in the production cycle, such as filling time, cooling time and painting time. There will be cold lines, the key reason is that the temperature in front of the molten soup is too low, and when there are imprints, they overlap.
How to improve:
- If the thickness of the wall is too thin (design scheme or production), then the thinner area should be filled immediately.
- The appearance inspection is not easy to refill, the distance is far, closed areas (such as leaves (small tail), camshafts), closed areas, small arcs, and other types of filling.
- Reduce the charging time
- Disassemble and refill.
- Improve temperature.
- The temperature of the soup
- Check the composition of the aluminum alloy.
- Running away can be effective
- A vacuum pump device can be effective.
When producing a working pressure casting mold, not only the temperature of the zinc abrasive tool is controlled. There are also some key points. The mesh structure of the zinc alloy material can reveal information tone differences, surface damage and other problems.
Selection and Melting of Zinc Alloy Die Casting Raw Materials
- Control the composition of zinc alloy materials From the beginning of purchasing zinc alloy material ingots, zinc alloy material ingots must be made of high-purity zinc plus extra-high-purity aluminum, magnesium, and copper, and manufacturers with strict composition control standards must be selected. supply. High-quality raw materials are the basis of famous products.
- The storage area of raw materials purchased for the home should be kept clean and dry. Be very aware of the hazards to the placement area when the weather changes. The corrosion resistance of zinc alloy material ingots is weak, and it will be corroded and cause white rust in the wet and cold natural environment for a long time. If the placement area is not cleaned properly, the zinc alloy material ingots will be polluted by the environment, which will increase the slag during smelting, and will also increase the consumption of the zinc alloy material. Clean, dry and placed natural environment is indispensable for the control of the purity of zinc alloy ingots.
- The proportion of returned waste such as pellets, nozzle materials, and waste parts. The proportion of returned waste is not suitable to be too high. Under normal conditions, pellets account for 70%, and scrap processing accounts for 30%. In the whole process of aluminum die-casting, the surface layer of the returning waste such as nozzle material is oxidized by air, and the composition of active zinc oxide is much higher than that of the original zinc alloy material ingot. When the returned waste is remelted, because the active zinc oxide is thick at high temperature standards, when the active zinc oxide is removed from the zinc pot, zinc, magnesium, etc. in the aluminum alloy will be taken away. Reduce the proportion of zinc and magnesium in the zinc pot.
- In the case of nozzle material and waste remelting, the remelting temperature must be strictly controlled and the remelting temperature should not exceed 430°C. Excessive temperature will greatly corrode tongs and special tools, resulting in damage to aluminum alloy components.
Conclusion
For more information about vacuum die casting machine,sipra die casting,aluminium gravity die casting process, we are glad to answer for you.