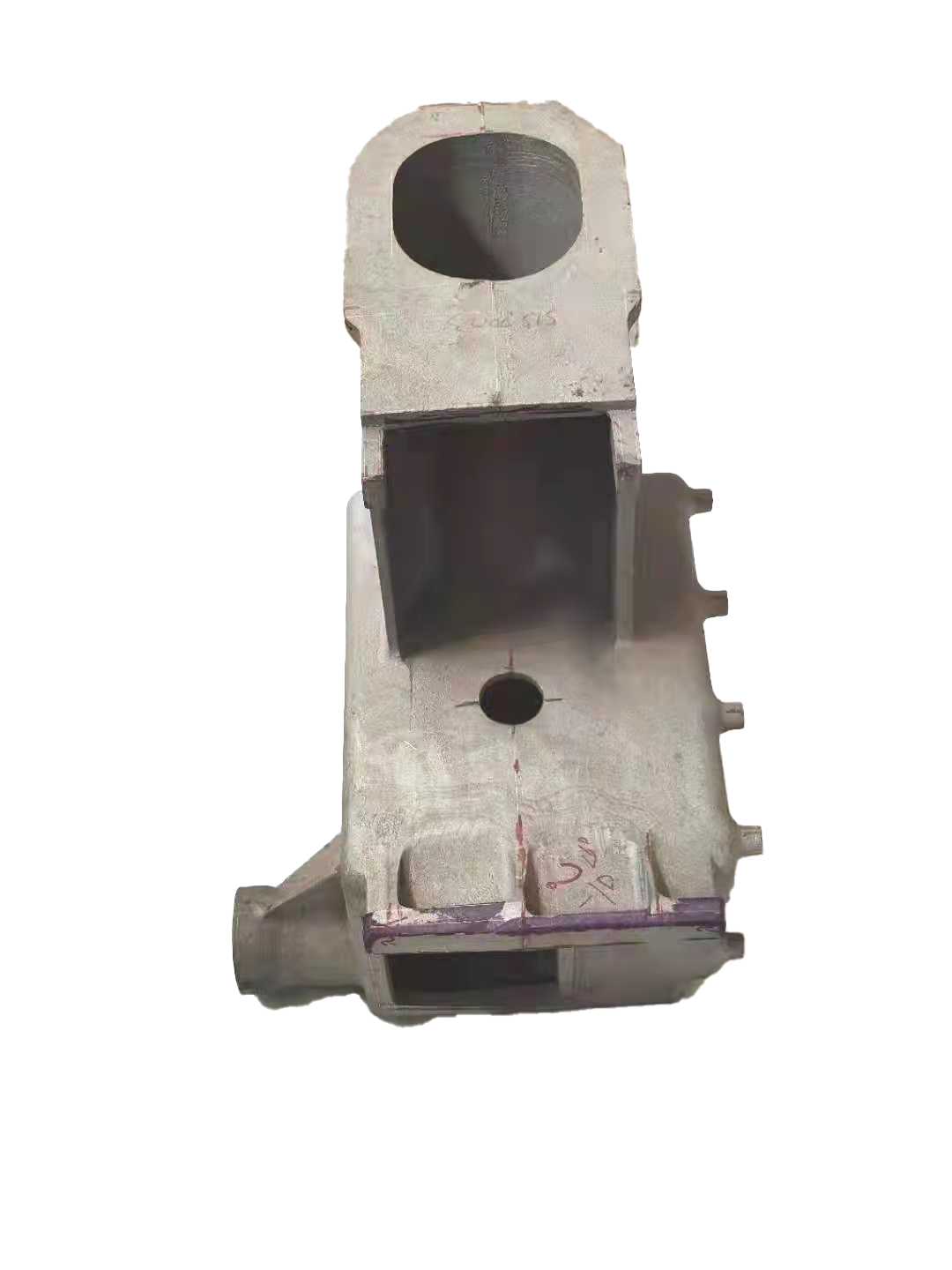
Common defect one:
Disadvantages of air oxidation welds: Air oxidation welds are mostly spread on the upper surface of the casting, at the corners where the metal mold is not ventilated. The fracture surface is mostly gray-white or light yellow, which can be found by X-ray fluoroscopy or machining, and can also be found in alkali washing, pickling passivation or anodizing treatment.
Cause:
- The returned waste is not cleaned up, and the demand for returned waste is too much
- Poor design of pouring control system
- The slag in the aluminum alloy liquid is not cleaned up
- The actual operation of pouring is not good, which leads to the welding bump
- Insufficient standing time after scouring and metamorphism
Ways to avoid:
- The returned waste should undergo sand blasting, and the demand for returned waste should be moderately reduced
- Improve the design of the pouring control system and enhance its slag blocking ability
- Use a moderate solution to remove slag
- It should be stable when pouring and should pay attention to slag blocking
- After scouring, the aluminum alloy liquid should be placed for a certain period of time before pouring.
Common defect two:
Disadvantages of vent bubbles: The vent holes in the wall of the three castings are generally round or oval, with a smooth surface, usually a luminous oxide skin, and sometimes oily yellowish. Surface vent holes and bubbles can be found by sandblasting, and internal vent holes can be found by X-ray fluoroscopy or machining. Air vent bubbles appear gray-black on X-ray film photographs.
Cause:
- The cast aluminum alloy is unstable and is involved in the vapor
- Organic chemical residues (such as coal dust, grass-roots entrepreneurial horse manure, etc.) infiltrated into the sand (core)
- Poor ventilation of metal molds and sand cores
- There is shrinkage on the surface of cold iron
- Poor design of pouring control system
Ways to avoid:
- Properly grasp the pouring rate to prevent the vapor from being involved
- The organic chemical residues cannot be infiltrated into the molding (core) sand to reduce the air supply of the modeling and design raw materials
- Improve the working ability of the exhaust pipe of (core) sand
- Proper adoption and solution of cold iron
- Improve the design of the pouring control system Three shrinkage porosity Disadvantages: shrinkage porosity of aluminum alloy die castings generally results in the thick position at the root of the fly gate around the inner sprue, the thin-thickness transition of the wall, and the thick wall with a large plan
Common defect three:
Crack Disadvantages Features:
- Forging cracks. Along the development trend of dislocation, it is often accompanied by shrinkage porosity, which is a kind of aluminum alloy with large volume shrinkage and complicated castings that are very prone to cracks generated at higher temperatures
- Quenching and tempering cracks: Transgranular cracks are often caused by the quenching and tempering treatment of coarse grains or over-temperature. Aluminum alloys with large in-situ stress and thermal expansion index are often refrigerated. Or there are other defects in the metallurgical industry
Cause:
- The overall design of the casting is unscientific, with bevels, and the thickness of the wall changes excessively
- The sand mold (core) has poor tolerance
- Overtemperature of the metal mold casting part
- The pouring temperature is too high
- Too early to remove castings from metal molds
- The quenching and tempering treatment is over-temperature or over-burning, and the cooling rate is extreme
Ways to avoid:
- Improve the overall design of castings, prevent oblique angles, and ensure uniform wall thickness and smooth connection
- Adopt measures to expand the tolerance of sand mold (core)
- Ensure that each part of the casting is solidified separately or in sequence to improve the design of the pouring control system
- Moderately reduce the pouring temperature
- Control the mold casting time of the metal mold
- The thermal calibration method is used when the aluminum alloy die-casting is deformed
- Properly control the temperature of the quenching and tempering treatment to reduce the cooling rate of the heat treatment
Conclusion
For more information about die casting auto parts,die casting automotive parts,shield aluminium die castings, we are glad to answer for you.